Tray Packing Applications in the Meal Kit Industry
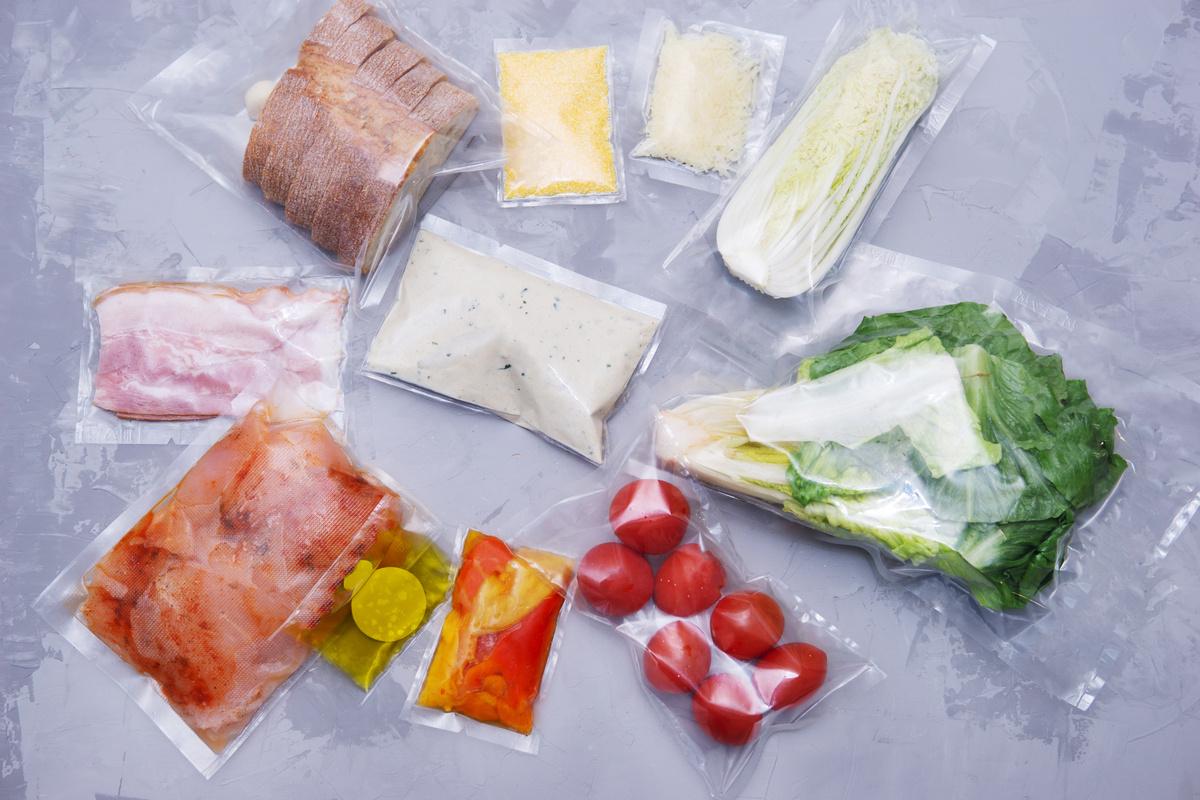
Whether delivered fresh to your door or picked up at the grocery store, ready-made meal kits have grown in popularity in the past decade as consumers search for convenient, time-efficient ways to eat healthily. While meal kits offer convenience and variety to consumers, they present significant challenges for manufacturers and co-packers.
Meal kit preparation and loading often include significant product variability and kit variation, making the processes difficult to automate. Automation is better suited for a high volume, low SKU mix where the lines can run longer. Still, many manufacturers can automate tray-loading applications when considering the layout and machinery used to support these processes.
We will explain how tray loading works and the challenges manufacturers face and explore options that enhance flexibility and efficiency while reducing labor dependence.
How Does Tray Loading for Meal Kits Work?
Meal kits go through an extensive loading process to ensure hygiene and quality control before they’re ready to go to the consumer:
- The process starts with bulk components fed from WIP and goes through a primary loading stage where various kit components are sorted and loaded into trays. These components could consist of naked products, like grilled or breaded chicken patties, and packaged components, like sauces and side items, that complete the meal.
- Once the trays are loaded, they are typically fed through a tray-sealer machine and then moved through a secondary packaging process, where they are packed into cases for palletization and distribution. A primary wall separates the primary and secondary loading processes to ensure hygiene and prevent contamination.
Manufacturers may start with a hybrid approach, having hand packers sort products and load the trays and then use a case packing system to perform the secondary packaging tasks. Or they could automate the entire process, incorporating robotics and vision into the primary loading and implementing additional case packing support from a different machine for downstream packaging.
Challenges that Could Impact Tray Loading for Meal Kits
Product variability and kit variation represent the most difficult challenges as they increase the likelihood of changeovers and complexities that negate the benefits of automation. Yet, other issues, too, will need to be addressed before a solution can be finalized. Here are some of the main challenges cited by our customers when they approach us about automating their tray-loading capabilities.
- Product Variability: Meal kits often include components of varying shape, size, weight, and fragility, creating complexity in consistent loading processes.
- Container Variability: Packaging may differ for a standard retail tray and club store tray format.
- Hygiene Standards: Manufacturers and co-packers must maintain strict sanitary conditions while handling cooked RTE or naked products.
- Changeover Efficiency: Frequent recipe updates or product variations necessitate quick system adjustments for different configurations.
- Alignment and Placement: Orientation of items, especially with irregularly shaped or soft products.
- Orientation: Product components could be loaded top or bottom, length-wise vs. short side into a container, etc.
- Damage Prevention: Avoiding product deformation or damage during high-speed operations.
- Labor Dependence: Difficulty finding labor for manual loading tasks, further amplified by increasing order volumes.
Automated Solutions to Improve Tray Loading Capacity
A wide range of machinery and accessories are available to support manufacturers and co-packers with meal kit production runs. Our goal is to help you find the right ones. At BPA, we consider the whole production process to recommend holistic solutions that minimize issues throughout. If there is a problem in primary loading, this could impact downstream processes and cause bottlenecks and delays.
Our solutions will consist of some or all of the following systems and accessories, depending on your facility footprint, loading stage, production goals, dedicated labor, and existing machinery and equipment. We want to ensure the systems know how to behave and are given the tools to perform the tasks effectively to justify the move toward automation.
- Loading systems: High-speed robotics, like our Spider 100v, are ideal for picking and placing multiple SKUs simultaneously and used in the primary loading side of the application. We also incorporate hygienic pneumatic and mechanical-style tooling in the loading process that is built to withstand powerful cleaning agents.
- Vision systems: Cameras and sensors can detect missing items, misalignments, or incorrect orientation. The robots will be programmed to know what products are acceptable and which should be placed in integrated reject stations. Weight checks can also be performed to verify the components within the tray.
- Secondary packaging machines: Our downstream systems can handle various tray formats and sizes once the meal kit tray has been sealed, bagged, cartoned, or wrapped. These systems can be robotic or Gantry-style and can be used to pack standard retail RSC shippers, club store display trays, and our Easy-D shelf-ready display case.
Additionally, BPA systems can incorporate modular designs that support rapid toolless changeovers and adapt seamlessly to different tray dimensions and materials. We offer customizable tooling and grippers to accommodate varying meal kit recipes, ensuring compatibility across a broad range of products while minimizing the chances of damaging the product during the presentation or loading process. Finally, our intuitive HMI panels allow operators to reconfigure production lines with minimal downtime.
Wrapping Up
Given the challenges we cited and the growing popularity of meal kits, food manufacturers and co-packers must carefully consider their primary and secondary loading requirements to ensure efficiency and quality control. Manual picking and placing is still viable, especially for short, low-volume runs with many components. Yet, automated systems can provide numerous benefits, including quality control and high-speed capabilities.
Partnering with packaging experts like BPA can ensure you have the right hybrid or fully automated approach to address your most pertinent challenges while experiencing the reliability and flexibility of automation. Our Sales Engineers can assist you in this selection stage to ensure you find the right solution for your production requirements. Contact us today to learn more about BPA’s tray-loading systems and capabilities.