From Manual to Automatic: Improve Your Tray Loading Capabilities with Automation
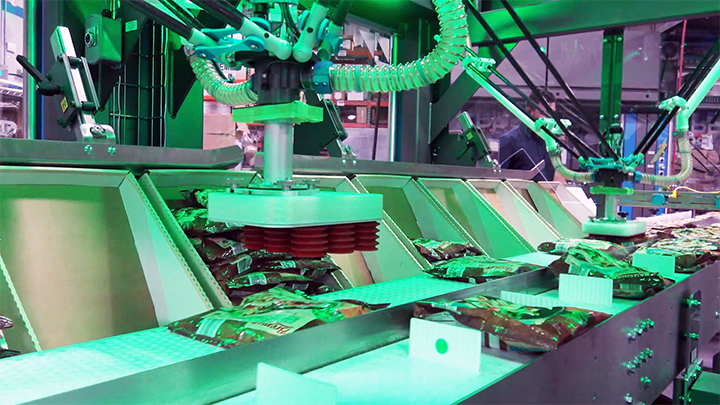
Adding an automated tray loading solution to your line can increase productivity while improving worker safety, reducing product damage, and decreasing downtime.
If you have automated upstream processes or need higher throughput to meet demand, an automated tray loader can help you reach your production goals.
Still, we understand that adding an automatic tray loader is a significant investment and could alter your operations, especially if your floor operators are used to manual tray loading.
Learn more about the purpose of an automatic tray loader, how it could benefit your line, and what you should know or provide to an equipment supplier to find the best solution for your secondary packaging needs.
How Does an Automatic Tray Loader Work?
Tray packaging is used for many different products (including edible food items), comes in a variety of sizes, and is made from various materials, depending on the intended application.
A tray loader (or tray packer) is used to load products into trays. If you’re familiar with a carton loader, a tray loader will run similarly, loading trays horizontally or vertically for distribution. Automated tray loaders can be found in high-volume production environments where speed and efficiency are paramount.
Tray loaders serve many different product lines and industries. They can place baked goods onto baking trays, load bars and snacks into display trays, pack frozen goods into trays quickly to retain freshness, and more.
How Do We Recommend the Right Tray Loader for a Packaging Line?
When a client comes to us and wants to use trays rather than regular slotted containers (RSC), we will recommend a solution based on their unique needs.
- For example, if product weight is a concern, we may recommend a Gantry-style tray loader that can handle heavier product payloads.
- On the other hand, if the solution requires precise picking at higher speeds and the product is presented to the robot in random order, we would likely recommend a sophisticated robotic tray loading solution integrated with a vision system.
If we work with a co-packer who incorporates many different recipes, we will look for a system that offers the most versatility and flexibility to meet their needs. Many tray loaders, for example, can pack a multitude of products and flavors from the same line.
Some of the most common and effective tray loading solutions we offer include the following:
- Gantry 300: High-speed vertical and horizontal tray loading capabilities with two axes. Better for heavier product loads, quick changeovers, and less linear floor space than larger robotic lines.
- Spider 100V: Replaces a traditional collate and load system and eliminates racetrack collation and potential jam points. Better for higher speeds, orientation, and quality control as the Spider 100V features an integrated vision system for maximum versatility.
When looking for the right tray loading solution for our clients, we will review various factors, including budget, floor space, line speed, product weight, and whether products come random and unoriented through the feeding system or orderly and in a single lane. There are many options, and you’ll want to have one specific to your needs.
What Are the Benefits of Using Automatic Tray Loaders?
Tray loaders have many benefits, including increased productivity and floor safety. Tray loaders excel in high-speed environments. They can run 24/7 with the same consistency and are designed to reduce downtime. You can reduce your reliance on manual labor operators for picking and packing and reallocate their efforts or retrain them for higher-order priorities. By reducing numbers, you can avoid congestion and floor safety issues that could impact your operations.
Tray loaders can also be customized to fit the specific needs of your production line. Whether you need to weigh products, test for counts, or load trays into cases, we can add crossover functionality to enhance quality control or integrate OEM to provide a complete erect load and seal line. No matter your specific needs, there’s a tray loading solution that can help you increase efficiency and productivity.
Tray packing is versatile. You can load one product or various products into one tray or multiple trays with an automatic tray packer. Robots can place a particular item into the tray (i.e., a dinner tray kit) or load a predetermined count, forming a pattern inside the tray. Overall, tray loaders can be used by processors and co-packers of all sizes, work with various product types, and can be configured to operate in tight floor spaces.
Tray loaders are easy to use and operate. When you partner with a reputable company like BluePrint Automation, you will receive the training your team needs to operate the equipment quickly and effectively. For us, training is provided during installation and site acceptance. Classroom for all shifts is optional. Our human-machine interface (HMI) was designed to be user-friendly and ensure simple and fast adoption. In the Americas, we also offer an Asset Health and Reliability Program to ensure equipment performance and reduce maintenance requirements for your operators.
Safety is built into the design of automatic tray loaders. Our equipment is designed with safety interlock door switches that will shut the machine down when the door is opened. There is guarding to eliminate pinch points and safeguarding conveyors to prevent finger trapping. During training, we will review safety best practices when operating our equipment.
How Can I Get Started with Tray Loading?
You can do a few things to make integrating a tray loader into your line successful:
First, you’ll want to do your homework upfront to confirm your final package and secondary case designs. You will also need to determine and provide the product rates you wish to achieve, the layout of your facility, how much space you need, your budget, and your company's safety and sanitary requirements.
Next, you’ll want to consider who you want to work with. As many options are available, finding a partner who can match your needs with the right automatic tray loading solution is essential to achieving your desired throughput and efficiency. As a global tray loading equipment manufacturer, we can tailor a solution based on your requirements and facility.
Wrapping Up
Blueprint Automation offers leading tray loading solutions that utilize simple two-axis Gantry-style machines or sophisticated robotics to optimize your tray loading and packing capabilities. Check out our BoxForm 300 tray erector as a complement to our automatic tray loaders. As every line is different, we encourage you to reach out to us to explore your options and our solutions. Contact us today to get started.