Everything You Need to Know about Automatic Case Packing
Have you outgrown your manual case packing methods and need to improve your packaging productivity and efficiency? Are high labor costs and inefficiencies hurting your bottom line? Automatic case packing is a viable option for manufacturers of all sizes who want to scale and futureproof their secondary packaging operations.
Automatic case packing involves packing products into cases using a machine, reducing dependency on manual packing processes. It has evolved to address various secondary packaging challenges, including higher production speeds, large quantities of products, complex pack patterns, and new packaging types.
Advancements in technology, from servo motors to vision guided robotics, have increased the flexibility and precision of automated case packing systems, enabling them to meet the needs of manufacturers and co-packers at a sustainable price point.
Still, adopting an automated solution starts with a good understanding of how automation works, the styles of case packers available, and the costs and responsibilities associated with ownership. We will delve into these topics to help you choose an automated case packer that fits your needs.
Determining the Right Level of Automation for Your Facility
We offer three levels of secondary packaging automation solutions to meet our customers’ objectives and comfort levels with automation. Start-ups and smaller companies, for example, will likely not need a fully automated solution to handle a single bagger or low volume of product flow. Each level of automation we offer removes a step of manual tasks in the process.
- In a semi-automatic system, humans are still required to place the product into the box, but machinery makes the process easier. An example of this is our Collator 200.
- Standard automatic systems can pick and place products, but the tasks for erecting and sealing the boxes are still performed manually. An example of this is our Gantry 300 Swing.
- Fully integrated systems automate everything—from erecting and sealing to palletizing—removing all manual steps and representing a significant leap in complexity and investment. Explore more about this on our website.
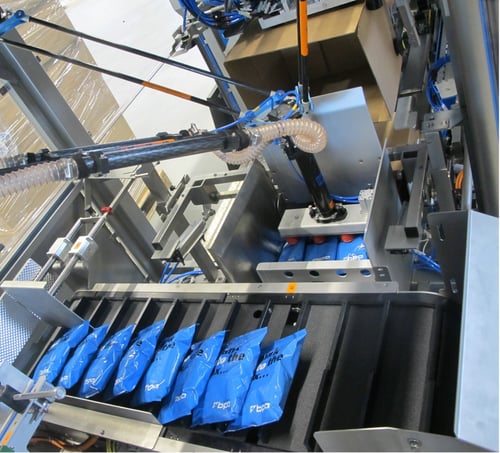
As we learn more about your operational capabilities, facility space, and organizational infrastructure, we will recommend the appropriate level of automation that aligns with your company’s goals and production needs.
How Does a Case Packing System Work?
We strive to make our case packing systems as flexible as possible to accommodate various facility layouts and production lines. Each system follows a similar flow that integrates the case packing process, from infeed to palletizing. By understanding this organized flow, manufacturers can optimize their case packing operations and improve overall productivity.
- Product Infeed: Products are conveyed from upstream processes into the case packer, and case blanks or formed RSCs are fed into the machine to load the products into a case.
- Collating: Products are then collected and arranged into predetermined pack patterns so each case retains the same organization.
- Loading: Products are loaded into cases using gravity to drop them into the case or arms to pick and place them. Depending on the pack pattern, some cases may require an extra manipulation step to tip or adjust the box's position.
- Sealing: The cases are then conveyed and sealed to ensure they remain secure during transport and storage. This may be done manually or automatically based on the system and level of automation selected.
- Palletizing: Finally, the cases are conveyed to a palletizing station, where they are stacked onto pallets for distribution to retail stores.
Selecting a Case Packer Style for Your Line
BluePrint Automation offers a wide range of case packers to boost our customers’ secondary packaging capabilities and meet their production goals.
Gravity machines represent the simplest case packing system. They utilize gravity to drop products into a secondary container, which is then pushed into the box. This method works well for products that settle easily, such as frozen vegetables, chicken nuggets, beans, flour, sugar, and bird seeds.
Two-axis Gantry-style case packers use an arm to pick and place products into cases, both horizontally and vertically, on the same system. This method lifts the product instead of using gravity, making it ideal for snack foods. It is also capable of handling heavier loads than systems with sophisticated robotics.
Case packers with delta-style robotics and vision guided systems are the most advanced systems for on-the-fly pick and placement of products with precision. They support high-speed and complex applications, like variety packs and high-speed carton loading, and are designed to fit your process entirely.
Finally, Wrap Around case packers are designed for rigid products and containers. Instead of placing the product into a pre-formed box, this integrated system creates a box around the product, providing an efficient packaging solution for certain applications where an RSC isn’t available. Our Easy-D retail-ready packaging, for example, can be loaded using a traditional top load or wrap around case packer.
Best Practices for Maintenance and Ownership
Our case packers are heavy-duty machines built for reliability and high-speed efficiency, but they require ongoing maintenance and support to ensure peak performance and longevity. Like an automobile, users need to follow the maintenance schedule in the manual and perform regular inspections and repairs to prevent more significant issues and equipment failures. We encourage our customers to consider the following best practices to keep their machines running efficiently.
Ensure Remote Support Access: Purchase a modem for your equipment and control cabinet. This enables technical support staff to troubleshoot and control the system remotely, reducing downtime and issue response times. HMI notifications and regular inspections can help determine if your equipment needs troubleshooting.
Implement a Preventative Maintenance Program: Every plant must take ownership of maintenance to ensure long-term success. This includes regularly reviewing the equipment manual to identify necessary maintenance tasks such as cleaning air filters and other components, greasing rails and axes, and inspecting and replacing vacuum hoses. It will likely also involve regular staff training, which we can assist with.
Schedule an Onsite Maintenance Visit: Many equipment manufacturers, including BluePrint Automation, offer customizable service contracts tailored to customer needs. For new customers, a baseline inspection every six months can help establish effective maintenance procedures and foster program ownership.
Wrapping Up
Automatic case packers will give your business a competitive edge by increasing productivity and efficiency. No matter your industry, there is likely a system that can help you meet your packaging needs, whether you’re just starting with automation or want to scale and upgrade your secondary packaging operations.
As a leading manufacturer of automatic case packers, we can help you select the solution and method that makes the most sense for your application. Contact us today to get started with automating your case packing process.