How to Reduce Bottlenecks for Mixed Production Runs
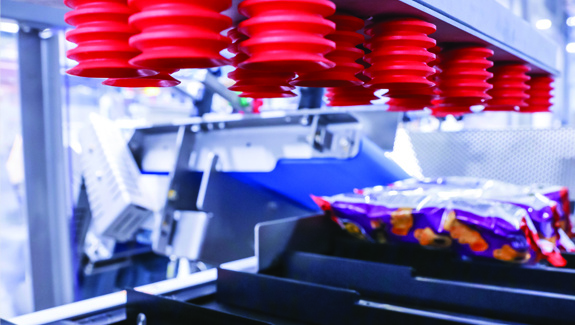
Mixed production lines are becoming increasingly common among snack industry manufacturers and co-packers to meet consumer preferences and diverse retailer demands. However, mixed runs present unique challenges that facilities must address as early as possible to minimize bottlenecks. From frequent changeovers to handling complex pack patterns, these secondary packaging challenges require strategic planning and dedicated solutions to maintain efficiency.
We’ll explore the most common types of product and packaging variations that can impact throughput and add complexity to secondary packaging operations. Then, we’ll provide tips on implementing equipment solutions and process improvements to optimize mixed production lines.
Common Variations in Mixed Runs
Mixed runs can involve different product configurations on the same packaging line. Here are some of the most common variations we’ve seen in the snack industry:
Variety Packs
Consumers desire multiple flavors and product types in a single package, which can be achieved through variety packs. Assorted snack bag cases or mixed bar packs present challenges in packaging as they require combining multiple products into one system while maintaining the correct count and mix of products. Solving these challenges can involve several layout strategies based on footprint and equipment.
.
Mixed Product Weights
Snack manufacturers often run different package sizes on the same line to increase throughput and efficiency. For example, a single production line might simultaneously handle the packaging of individual 1 oz. snack-size pouches, 16 oz. club-store packs, and 10 lb. bulk packaging intended for restaurants.
Packaging Types
Snack packaging comes in a variety of formats to meet different market needs. Flow-wrapped pouches are standard for bars and crackers, while resealable bags work well for nuts and trail mix. Larger bulk bags cater to institutional buyers, and rigid trays protect delicate snacks like cakes and muffins. Addressing these packaging variations can quickly become complicated when packing them into cartons or cases for distribution.
Packaging Formats
Packaging formats also vary based on retail and distribution requirements. Single-flavor and multi-flavor variety packs are popular in grocery stores, while club stores often have three-sided display cases for easy grab-and-go. Large-format bulk cases streamline handling for restaurants and food trucks, and display-ready cases with easy tear-off panels improve in-store presentation. Different formats could also impact equipment selection and layout.
Private Label Packaging
Co-packers frequently run the same product under multiple brand labels, which may require different packaging materials and formats. They will likely have unique barcoding and labeling requirements that can add complexity, too. These variations can lead to increased downtime if labeling and packaging equipment cannot adapt quickly.
Bottlenecks That Can Impact Mixed Runs
Adding more variations to the production line will also add complexity and challenges. Addressing these issues upfront will help to minimize downtime and other adverse impacts that could affect production and revenue.
- Changeover Time and Manual Labor: Shifting between different packaging sizes and formats will require adjusting infeed systems, end-of-arm tooling (EOAT), and software settings. Many of these adjustments are still done manually, which could lead to inefficiencies and errors.
- Complex Pack Patterns: Certain snack products require specific orientations or patterns within a case to meet retailer requirements. These can be done manually or by robotics, but some systems are not always optimized for handling multiple orientations seamlessly.
- Inflexible Equipment: Some legacy systems aren’t designed to handle different product types and packaging formats, requiring manual intervention or additional machinery to fill the gap. This could be difficult, especially if floor space is at a premium.
Despite the challenges, mixed runs may be necessary for many manufacturers and co-packers due to space constraints, retailer and consumer demand, maximizing equipment utilization, and short-term contracts. Next, we’ll review some proven solutions and improvements to optimize secondary packaging operations for product variations.
Strategies for Managing Mixed Runs and Reducing Bottlenecks
Whether a snack manufacturer or co-packer chooses to implement a completely new variety line or a minor upgrade to an existing system, they can improve their results by implementing some or all of the strategies outlined below. Our experts can help facilities select and prioritize strategies to accommodate mixed runs and achieve better results.
Selecting Flexible Equipment: When possible, manufacturers and co-packers should always consider what priorities they have now and where they may be in the future to ensure their systems can accommodate those new needs. Here are a few examples of futureproofing secondary packaging machinery:
- Robotic pick-and-place systems, like the Gantry 300 Swing, with adaptable tooling for multiple pack configurations. The Gantry 300 Swing can create vertical and flat packs on the same line for increased flexibility during mixed runs
- Modular machinery and flexible layouts to fit within compact footprints
- Automated changeovers with programmable settings for different SKUs
- Adjustable conveyor side rails and buffers to accommodate different product sizes and minimize downtime
- Vision systems to detect product variations and adjust packing accordingly
Optimizing Production Schedules: Rather than switching frequently between different products, manufacturers can adjust schedules to avoid complicated changeovers, especially if they can’t immediately implement automation. Modifying the production schedule based on product type and packaging format could include these strategies:
- Separating production by shift, like running snack-size packs in the morning and bulk packs in the afternoon
- Storing individual SKUs in bulk bins and packing variety packs in an offline process rather than integrating them into a live production run
Improving Employee Training and Preventative Maintenance: While minimizing manual processes will reduce errors, human operations will still be required for any automated solution. Packaging facilities can reduce bottlenecks and improve equipment longevity by being proactive in training and maintenance and ensuring the following:
- Comprehensive training for operators on machine settings and changeovers
- Clear documentation and manuals on all relevant processes and equipment
- Real-time monitoring to assess system performance and improvements
- Preventive maintenance integrated into SOPs to keep machinery in peak condition
Wrapping Up
Running mixed production lines often feels like a balancing act between flexibility and efficiency. We’ve listed the possible product variations and bottlenecks that could impact both. Still, we’ve also hopefully shown how manufacturers and co-packers can proactively address challenges that impact productivity and revenue. As a dedicated partner, BPA can help you determine the right strategies and solutions to meet the growing demand for variety packs and different packaging sizes. Let’s explore the endless possibilities to enhance your capability to support mixed runs today.