EOAT Methods for Primary Packaging Applications
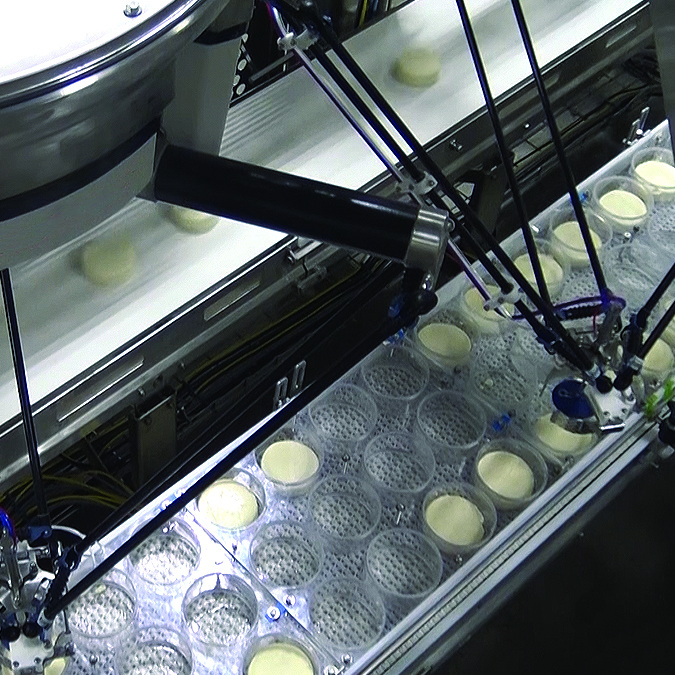
Manufacturing plants that require more flexibility and speed from their primary packaging process are increasingly looking at automated solutions. Primary packaging involves placing raw or naked products into flow wrappers, H/F/F systems, pouches, containers, or trays for the first layer of packaging. Careful consideration must be given to handling and packaging to ensure the integrity of the products while maintaining high speed and safety standards.
Advanced robotics paired with a vision system reduces reliance on manual picking and placing, which can be inconsistent, costly, and increase sanitation risk. End-of-arm tooling (EOAT) refers to the devices at the end of the robot used for various tasks for a primary packaging system, including lifting, handling, and placing any raw products. It is a critical component of robotics as it acts as the “hand” of a robot to perform actions that would otherwise require human intervention.
Choosing the right EOAT for your primary packaging will depend on the production run, as different devices are more suitable for specific applications. The size, shape, texture, weight, and fragility of the products being packaged should be considered so the strengths of the EOAT align with the application requirements.
At BPA, we incorporate various EOAT for our robotics, including vacuum blower tooling, venturi-style vacuum suction cups, and mechanical gripper-style tools for handling raw products efficiently and safely. We will explore these three types of EOAT to show how they can enhance your primary packaging automation strategy and increase your process flexibility and accuracy.
Vacuum Blower EOAT for Flat Products
Thin, lightweight baked goods, like pancakes, waffles, tortillas, and crackers, require gentler handling to be placed into their primary packaging. Vacuum blower EOAT uses low-pressure, high-volume air to delicately lift and move these flat products into their packaging without damaging them.
Depending on the application, stacking and non-stacking tooling are available to meet the run’s packaging requirements. Our stacking EOAT, for example, is designed to create uniform stacks of products for primary packaging. The robot can follow and recognize the shape of the products and adjust the tooling to hit that shape in between picks.
How Do Vacuum Blower EOAT Work?
A large vacuum blower spreads a high volume of low-pressure air to gently lift and hold objects. The EOAT we use for this method consists of a patented 3D-printed canister with ridges around it that allow the vacuum to flow around the edges of the product. The product does not stick to the tool, but there is enough of a constant updraft of air to hold it into place once the arm moves over it. The product is then gently pushed out once the robot moves it to its designated location.
Venturi EOAT for Raw Proteins
An EOAT method commonly used for handling raw proteins in primary packaging systems is venturi suction. Venturi suction involves compressed air used to lift and handle slippery and flat surface naked products, like raw chicken, frozen fish filets, and corn dogs, which are then loaded into a tray or other packaging format.
Venturi systems are often preferred when products can’t be gripped. However, the product must have a flat or uniform surface for the cup to latch to it. The compressed air system creates suction while pulling moisture and debris out to prevent clogging.
How Do Venturi Systems Work?
Venturi systems force compressed air through a small nozzle, creating a vacuum from the accelerated air. The vacuum generates enough suction pressure through the cup to securely lift and handle the protein without tearing or deforming it. Once it's lifted carefully, the EOAT’s food-grade suction cup will hold the protein until it's ready to be placed in the correct position. Venturi systems blow excess liquid or debris right back out to ensure suction performance.
Mechanical Grippers for Irregularly Shaped Products
The last EOAT method we will focus on is the one that most resembles an actual hand. Mechanical gripper-style tools are designed to handle irregular and heavier products unsuitable for vacuums. Bone-in meats, drumsticks, muffins, and whole vegetables are some of the most common naked products mechanical grippers can handle, ensuring a secure hold while minimizing the risk of crushing or damaging the products.
Depending on the design, mechanical grippers can use fingers, clamps, or gripping pads to physically grasp the products and move them to the primary packaging area.
How Do Mechanical Grippers Work?
Once the robot identifies the product that needs to be picked and placed, the arm moves the gripper above the product, adjusting the fingers or clamps to the expected product size. Pneumatic or servo-driven actuators power the gripping mechanism, which closes around the product and applies controlled force to secure it without crushing it. When ready, the gripper opens to place the product in the correct orientation and position for packaging.
Grippers can be designed with adaptive or soft-touch materials to prevent product damage during handling. We often design and fabricate in-house gripping options to ensure the proper fit for a specific product or application.
Wrapping Up
Depending on the application, BPA can help you determine the optimal EOAT to support your robotic solution. With an advanced primary packaging system, like our Spider 100v, EOAT ensures products are identified, picked, and placed for a continuous flow to support your packaging needs. Our solutions also involve toolless changeovers to minimize downtime as different products run through production.
Our Sales Engineers can help you assess your needs and determine the right EOAT to support your production goals. They can also educate you on maintenance and upkeep practices to comply with all applicable food safety regulations and guidelines in your industry. Contact us today to discuss ways to improve your primary packaging capabilities for speed, accuracy, and flexibility.