Modular Secondary Packaging Systems for Improved Scalability
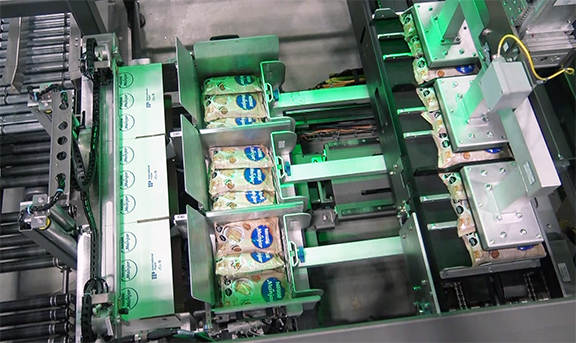
As consumer preferences change and retailer requirements continue to evolve, manufacturers must be able to adapt to maintain and grow their business. Whether they need to diversify their product lines or introduce a new packaging format, having the right secondary packaging equipment is crucial to ensuring efficiency and productivity.
Automation helps manufacturers increase speed and uptime while minimizing labor inefficiencies. Yet, any manufacturer faces a difficult question when considering a secondary packaging solution: How do we invest in automation that helps us today but is ready for tomorrow’s uncertainties?
We frequently recommend modular product packaging systems to our customers to solve this challenge. This flexible approach to automation offers many advantages in scalability and operational resilience that will help them adapt to evolving market conditions and meet their growing needs. We will explain how modular packaging solutions work and our approach to finding the right solution to scale with you.
What is a Modular Product Packaging System?
Unlike an all-in-one solution where multiple process steps are handled by one machine, a modular product packaging system divides the packaging process so separate pieces of equipment handle different functions. This modular concept can apply to various secondary packaging applications, including case packing, where products are packed into shipping cases, or carton loading, where primary products are loaded into smaller cartons.
While each modular solution will be slightly different based on the customer’s needs, here are some of the most common components that will work together to move products from primary packaging and make them ready for distribution:
- Case Erector: This machine takes flat corrugated case blanks, forms them into shape, and seals the bottom flaps with tape or glue, presenting an open case ready for product.
- Conveyors: Conveyors transport products throughout the system. It starts with infeed conveyors that move products from upstream processes to the secondary packaging line.
- Case Packer / Robotic Packing Cell: This is where products are loaded with a case packer, like our gantry-style and gravity offerings. For some applications, we can install advanced robotics in these cells for complex pick-and-place functions and precision handling.
- Case Sealer: Once the case is packed, it is sent to a sealer, which closes and securely seals the top flaps of the filled case.
- Labeler / Printer: This machine applies necessary shipping labels or prints variable information onto the sealed case before it is palletized.
Depending on the system and customer preferences, we may include a weight scale or other components to ensure quality control, handle palletizing, and other functions.
Why Do Manufacturers Choose to Go Modular?
As we hinted above, scalability is one of the primary drivers for choosing a modular secondary packaging system. The system can be adjusted or equipment added to ensure it evolves with a customer’s needs for volume, packaging format, budget, and more. We broke down some of those needs and challenges below:
- Operational Resilience: Modular systems offer more ways for a system to stay running even if a functional station goes down. For example, if there is an issue with the case packer or packing cell, hand packers could still pack the product into cases until the issue is resolved.
- Volume Scalability: A modular system can be used to pack more cases. Robotic cells can often be scaled up by adding another robot. Conveyors can be designed slightly longer initially to account for future growth. A single module becoming a bottleneck can be replaced with a faster one, rather than replacing the entire system.
- Format Scalability: Modular systems are easier to adapt if a customer needs to handle different product sizes, pack types, case dimensions, and pack patterns for specific retailer requirements. Changes might involve reprogramming recipes, swapping robotic end-of-arm tools, or adjusting training to accommodate different formats.
- Functional Scalability: Want to add vision inspection or checkweighing later? These functions can often be incorporated as additional modules within the line's flow.
- Economic Scalability: Modular design allows for phased investment. Customers can start with specific modules to meet their current needs and add capacity or functionality later when it is more cost-effective or required.
Modular systems offer greater flexibility, even if a customer is unsure what their line will look like in five years. Of course, our sales engineers will help customers identify possibilities to plan for and determine potential adaptations. However, modular systems offer more flexibility now and down the road to offset any uncertainties.
Comparing Modular Systems to All-in-One Solutions
While a modular system works in many environments, an all-in-one system may be a better alternative depending on facility space, budget, and customer preferences. At BPA, we design turnkey solutions to give our customers the most options for their secondary packaging line. For example, our wraparound case packer is an effective all-in-one solution that forms a case tightly around the product, packs it, and seals it within the same machine.
We took a deep dive into this debate, but it really amounts to what a customer is looking for and how well the solution’s benefits align with their needs. Modular systems offer more “Plan B” capabilities as the functions are separate, so the entire line won’t necessarily go down if one module has an issue. They are also easier to update and provide targeted maintenance.
However, all-in-one systems often have a smaller footprint because they involve one machine rather than interconnected components. There is potential for corrugate usage to be reduced due to tighter case wraps. All-in-one systems are also often theoretically more efficient, as multiple machines will impact OEE calculations. If three units for a modular system are 99% effective individually, they will be 97% effective when multiplied together.
Wrapping Up
Choosing the right automation strategy requires a deep understanding of these advantages and trade-offs and how they compare against your specific operational needs and future goals. At BPA, we emphasize a collaborative approach where we can be a true partner to our customers.
Our process starts with listening and understanding your core needs, future aspirations, and potential variations. Because we build various automated secondary packaging solutions for modular and all-in-one systems, we can objectively discuss the advantages of each system and compare them to your specific needs.
We incorporate our decades of experience and industry knowledge into our recommendations. Our engineers can utilize the latest technologies, like AI for preventative maintenance and cameras for remote diagnostic support, to ensure long-term success and adaptability. We collaborate with customers throughout the process to refine the solution for their environment and application.
Are you ready to explore how a modular solution can enhance your scalability and efficiency? Contact us today to discuss your challenges and goals.