Comparing All-in-One and Modular Packaging Systems
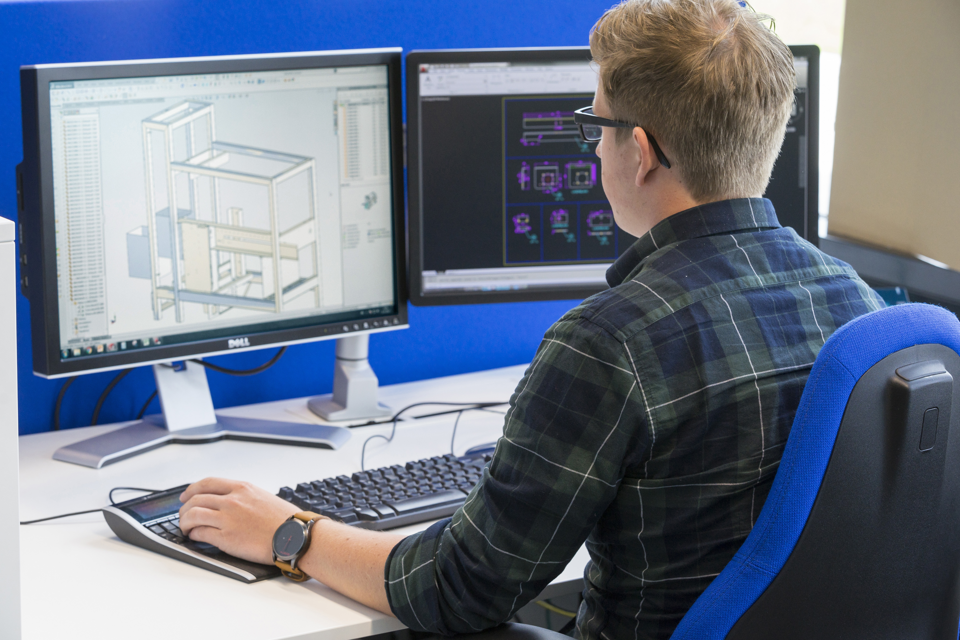
A new secondary packaging system that handles the case erecting, packing, and sealing processes can add significant flexibility, speed, and efficiency to a manufacturer’s secondary packaging operations. Still, every line is unique, with specific needs, production speeds, and packaging requirements. These, along with facility space, layout, and upstream performance, will impact a manufacturer’s selection when automating their secondary packaging processes.
Equipment manufacturers focus on two approaches for secondary packaging: modular systems and all-in-one systems. Each approach is slightly different, but in our experience, both represented in our packaging solutions offer similar cost-effectiveness, simple maintenance, and high performance. However, other factors may make one approach better fit your facility and operations.
As a starting point, we will break down some of the features and benefits of both approaches to help you identify which system may be more closely aligned with your present and future needs.
All-in-One Packaging Systems
An all-in-one packaging system is a fully integrated solution that handles multiple secondary packaging steps within a single machine. Most all-in-one systems will automate erecting, packing, and sealing processes to increase productivity and flexibility. As a whole, all-in-one systems offer a wide range of benefits to a manufacturer:
Consistent Performance
An all-in-one system synchronizes multiple packaging steps and is optimized for high-speed production. The erecting, packing, and sealing components run on the same control platform, ensuring smooth operation, alerting, and real-time operational adjustments. With an all-in-one system, each component is designed to be compatible, making it easier for the operator to control and troubleshoot the system.
Smaller Footprint
Many all-in-one systems have a compact design, enabling manufacturers to automate multiple secondary packaging processes with a smaller footprint than having a machine center handle each process. Depending on the facility's layout, an all-in-one packaging system may provide greater space efficiency for facilities with tight spacing.
Less Material Waste
Some all-in-one systems, like our Wraparound 300, can significantly reduce case size, cutting corrugate costs, which could mean significant savings in high-volume production. Wraparound case packing systems create tighter cases than RSC containers and are widely used in the dairy industry and for retail-ready display packaging.
Increasing Flexibility
Depending on the application, all-in-one systems are designed to support various requirements and layouts:
- Wraparound solutions allow products to come in from any direction. The case blanks can typically be loaded almost in any direction, and the finished case can exit out in any direction.
- In the snacks industry, all-in-one solutions are often used for chips and other bagged treats. The Spider 200i offers significant versatility to manufacturers, allowing them to run various product sizes and case types on the same line.
- Gravity solutions, like our CubeMaster 300i, are ideal for frozen foods. The CubeMaster 300i can operate both vertically and horizontally.
Modular Packaging Systems
A modular packaging system is the complete opposite of an all-in-one system. Each step of the packaging process is handled by separate, individual machine centers. In some facilities, the case erector may operate remotely from the case packer and sealer. While modular systems offer all of the benefits of automation as all-in-one systems, they have additional features that may be particularly useful for some applications and facilities:
Maximum Flexibility
Each component can be individually configured and upgraded in a modular system to accommodate various packaging requirements and new runs. It offers the highest level of customization for a packaging system as a manufacturer can mix and max components as needed, and each machine center can be arranged in any way to fit a facility’s existing layout. Having an individual component for each process often increases the footprint over an all-in-one system with a more compact design, but a modular system can be configured to fit the facility space more efficiently.
Reduced Risk of Downtime
If one part of a modular system goes down momentarily or requires attention, the rest of the machine centers can usually keep running, ensuring that production doesn’t entirely shut down. A manufacturer can repair and replace a downed component or modify individual components much more quickly than in an all-in-one system, where the entire system might need to be stopped to address repairs or modifications.
Troubleshooting and maintenance are typically easier for modular systems because technicians have more space to work, but we designed our all-in-one systems with ease of maintenance and repairs in mind. All BPA case packers and packaging components are heavy-duty machines that are easy to maintain, whether a customer opts for a modular system or all-in-one. Still, as technicians only need to focus on one component rather than an entire system, modular systems are inherently easier to troubleshoot and maintain.
Better Scalability
Whether a manufacturer wants to add a new product or increase production speeds, a modular system will offer more flexibility to make the necessary changes. For example, a co-packer benefits more from a modular system to accommodate new customers with various product types and packaging requirements. Manufacturers can easily swap or add modular components without replacing the entire system and adapt to new changes in the market faster and more cost-effectively.
Optimized Performance
As modular components can be individually selected and configured to meet individual requirements and packaging needs, manufacturers can use the best-performing components for individual tasks. As erectors and sealers typically can be run on-demand, integrations aren’t usually complicated, and manufacturers can focus on selecting the best fit for their runs. They can mix and match components for specific applications, like pairing a Gantry machine with a separate erector and sealer for frozen foods. This ensures that each part of the process is handled by a component designed for that application versus an all-in-one that offers outstanding performance and functionality but slightly less customization and optimization.
How to Determine Which System Is Right For Your Secondary Packaging Operations
The choice between an all-in-one and modular packaging system often comes down to customer preference. However, for specific applications and facilities, one system may provide additional functionality or flexibility to suit the individual customer's needs better. Our Sales Engineers can help you select the right system based on your production volume and speed, product type, packaging requirements, tolerance for downtime, facility space and layout, and operator expertise.
We encourage you to consider both options, as the right selection may not initially be apparent. BluePrint Automation offers high-quality equipment to support both approaches and ensure you have the best packaging system possible for your operations.
Wrapping Up
Each manufacturer is different, so we offer all-in-one and modular solutions to ensure performance and flexibility for many applications. All-in-one systems are consistent and work seamlessly together, providing a compact solution that could help you save on packaging materials.
Modular systems allow for greater flexibility and customization, ensuring you have the right individual components to meet your ever-changing needs. They may also be more accessible for troubleshooting and minimizing downtime than the all-in-one.
Contact us today to discuss your options and find the best packaging system approach.