How Risk Assessments Drive Higher Safety Standards in Secondary Packaging
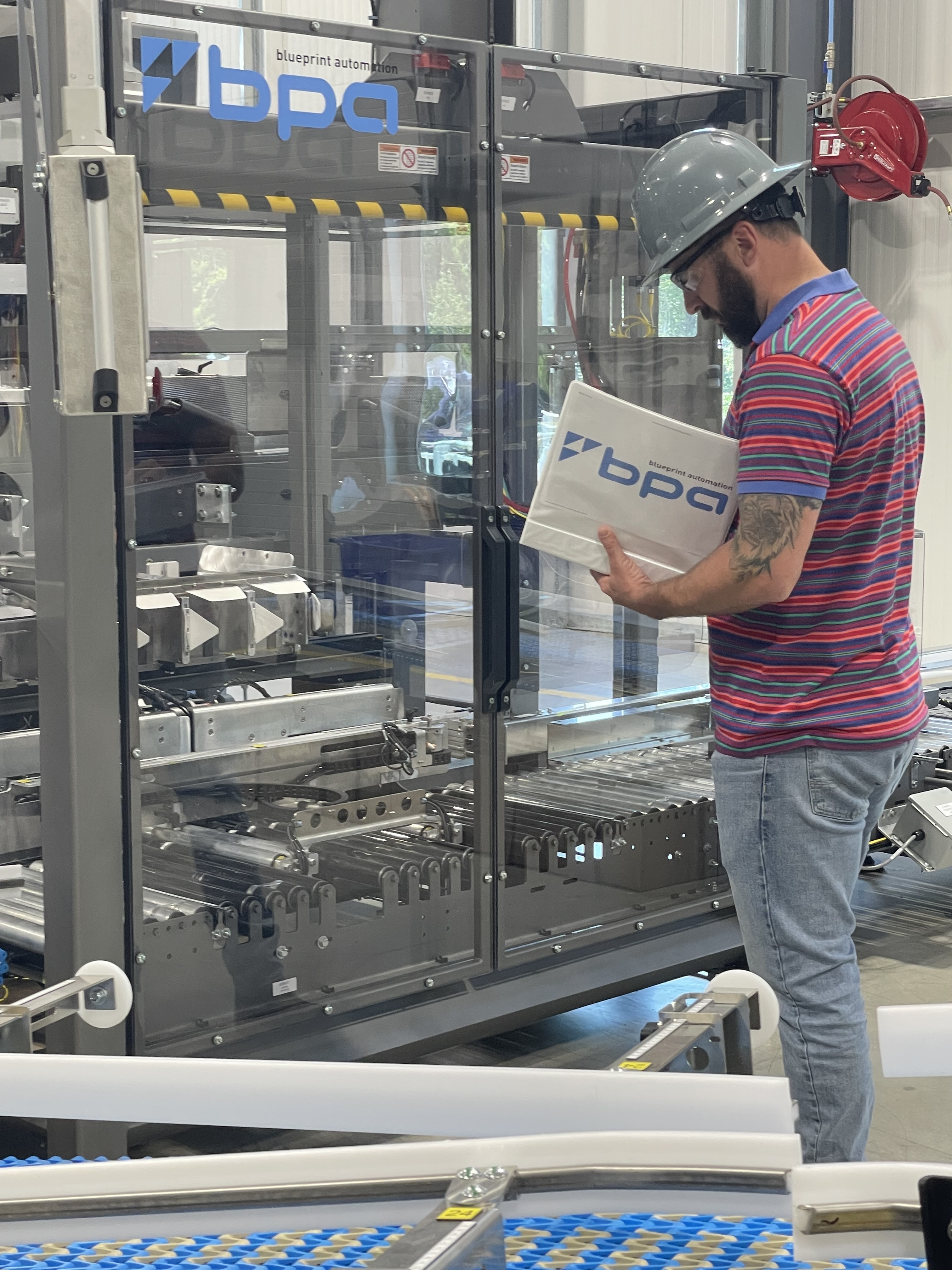
From the initial machine design to the final installation and ongoing support, BPA approaches everything with a safety-first principle. This philosophy drives our rigorous approach to risk management and safety system design. Risk assessments are an integral part of the engineering process and a proactive approach to managing risk and ensuring our machines' safety.
If you’re considering a new machine for your secondary packaging line or a critical modification to your current BPA equipment, we’ll explore the benefits of requesting a risk assessment for your upcoming project. We’ll also examine potential hazards that an assessment will help identify to keep your people safe when working with or on BPA machinery.
Understanding Potential Machine Hazards
Secondary packaging equipment involves many moving parts, energy sources, and processes that could pose dangers if not properly managed. During our initial assessment of our standard equipment, we examine every aspect of a machine’s operation to identify potential hazards, including the following:
- Mechanical Hazards: Common risks include pinch points where fingers or limbs could get caught, crushing zones created by moving components, shearing actions, and entanglement risks.
- Electrical Hazards: There is a potential for electrocution from exposed wiring or components and the danger of arc flash incidents, particularly during maintenance or malfunction, when failure to follow strict Lock Out Tag Out (LOTO) procedures to de-energize equipment can lead to severe injury.
- Reach-In Hazards: These are prevalent with pick-and-place systems, robotics, and conveyors, where operators might instinctively reach into the machine path to clear jams or adjust products, exposing themselves to moving parts.
- Robotic Hazards: Industrial robots operate with significant speed and force within designated cells. Risks include injury from impact and crushing, and the potential for staff to become trapped inside safeguarded spaces during maintenance or unexpected restarts.
- Ergonomic Hazards: While automation reduces many manual risks, poor design can introduce repetitive strain injuries, like carpal tunnel syndrome, or musculoskeletal issues from awkward postures or movements.
- User Hazards: Risks arising from lack of training, complacency developed through familiarity with the machines, or intentional overriding of safety measures, often during maintenance procedures.
How Do Risk Assessments Work?
When customers purchase a new machine or modify their existing BPA equipment, they can also acquire a risk assessment. A risk assessment’s core purpose is to identify any potential way someone could get hurt interacting with the machine, informing decisions on risk reduction and safety design modifications. Although there will be variations in risk assessments among manufacturers, most assessments incorporate some of the following elements:
Evaluating Hazards: The process usually begins by pinpointing the machine’s hazards without guards. Engineers will look for risks like pinching, crushing, electrocution, or arc flash. They will examine the machine, listing all conceivable dangers and staff interaction points. Before implementing guarding, engineers will likely explore design changes to mitigate those risks, like widening a gap or altering a component’s movement.
Analyzing the Human Factor: A risk assessment will also examine how staff must access the machine for troubleshooting and maintenance to ensure safety. This could involve considering the required operator training levels, labor turnover rates, and the risks associated with overriding safety measures. Robust training, clear standard operating procedures (SOPs), and safety measures like individually coded door keys can help mitigate these challenges.
Site Visits: For complex integrations or older systems, a site visit might be needed to determine the available space and other machines involved in the integration. This is especially important to our engineers for older non-BPA machines on the line with less formal documentation. They will examine the line and speak with site personnel to compile their findings for a tailored report.
Documentation: All findings will be compiled into formal documentation detailing hazards, mitigations, and compliance with the appropriate standards, like ISO 12100 and NFPA 79. Throughout our process, we partner with each of our customers to assist in risk assessments on our side during creation and encourage the customer to conduct a thorough risk assessment for their environment.
What Are the Benefits of a Risk Assessment?
By now, you probably know that the most crucial benefit of a risk assessment is enhanced safety for anyone who interacts with secondary packaging machinery. Risk assessments can help manufacturers and facilities implement a safety system that proactively protects people from sustaining injury from a previously unforeseen machine design issue or human error from a lack of training or poorly planned SOPs.
Beyond injury prevention, insights gained from a detailed risk assessment could improve machine reliability and increase uptime. Machines designed with safety integrated early on tend to be less prone to trips or breakdowns than those without safety features.
Also, the assessment process encourages consideration of better ergonomics, leading to designs that minimize repetitive strain injuries, musculoskeletal issues, and operator fatigue. Finally, rigorous risk assessments help ensure compliance with necessary industry standards and specific customer requirements.
How BPA Adds Safety to Secondary Packaging Equipment
Through our risk assessment findings, we integrate safety into the machine’s design by first modifying the machine to eliminate or reduce hazards. We will then implement physical guarding tailored to the specific hazard where risks remain.
Fixed guarding, like bolted barriers, can be built directly into the machine, while movable interlocks are typically used for access for maintenance and troubleshooting. Tunnel guards or presence-sensing devices, like light curtains and scanners, can help prevent operators from reaching into hazardous areas.
We complement our physical guards with robust control systems. We typically design to Category 3 and PLd standards to ensure a single component failure won’t lead to a dangerous situation. Additionally, we can incorporate advanced safety measures, like trapped key access systems and sequestered disconnects, when requested or warranted.
Trapped key access systems prevent staff from being accidentally locked inside safeguarded spaces during maintenance. Sequestered disconnects significantly improve electrical safety by isolating operators from potential arc flash incidents and ensuring the entire panel is de-energized for maintenance.
Wrapping Up
Our engineering-driven approach, emphasizing customization and flexibility, allows us to integrate the highest levels of safety appropriate for each unique application, often exceeding industry norms. Over a decade ago, we established Cat 3 and PLd as our standard. Taking the time to understand the application, collaborating openly, and prioritizing the safety of everyone interacting with our machinery is the foundation of our engineering philosophy.
Our design and controls engineers perform risk assessments for new builds as well as machine upgrades and modifications for existing BPA equipment, which our large Service Team handles. If you are considering implementing new equipment or modifying your existing case packer, a risk assessment is an essential safety tool that more than pays for itself through risk mitigation and improved uptime.
Contact us today to learn more about risk assessments and our approach to safety throughout the process.