How Can Robotic Case Packing Help Reduce Carbon Emissions
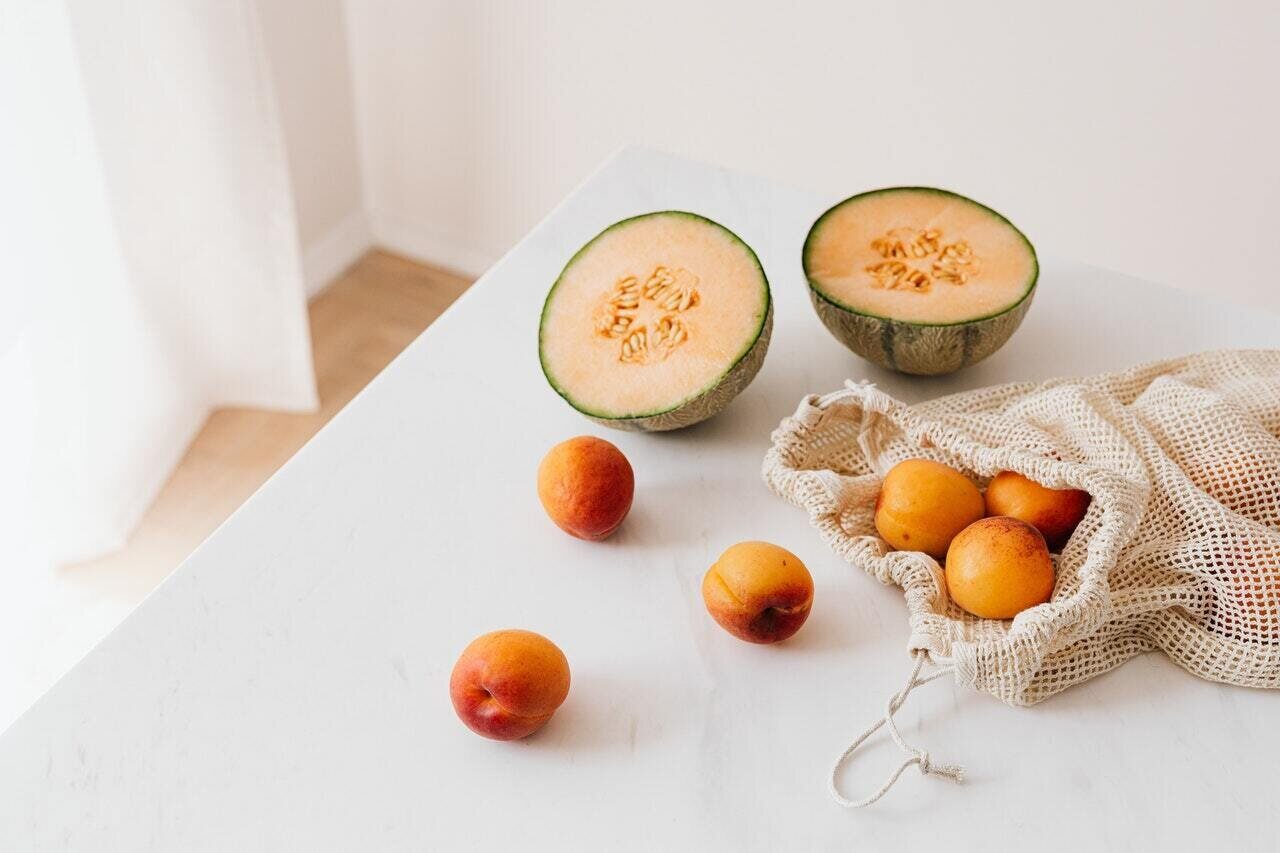
Ever heard of how it takes a village to raise a child? That was also true in the case of assembly lines and factories not too long ago. It took massive armies of highly skilled manual labor to turn raw material into the neatly packaged boxes we see at our local grocer.
Food processing companies are now integrating robotic case packing in addition to manual labor. That's helping food businesses boast profitability while increasing productivity and better managing the workloads of their workforce.
The Pandemic’s Effect on the Food Industry
During the recent pandemic, the thought of edibles packed by human hands didn’t exactly boost consumer confidence in food manufacturing brands. Robotic case packing is what helped many companies stay open and afloat.
Similarly, early robotics integration can help companies tackle the next big manufacturing challenge facing businesses all around the globe: reducing carbon emissions while remaining profitable.
An increase in single-use plastic and excessive use of fossil fuels have exacerbated damage to the environment. The packaged food industry causes a huge share of this. During the last 50 years, the delicate balance of nature has been utterly disrupted by our consumption and manufacturing habits.
Automation can be the critical component needed to help companies recoup from losses suffered during the pandemic. But, it can also re-build the $300 billion a year food packaging industry. Robotic incorporation can help create eco-friendly assembly lines. Which are more efficient in their work while offering more resilience against the next pandemic. Knock on wood!
Ways Robotic Case Packing Can Help Reduce Carbon Footprint
Robotic case packing equipment can streamline operations dealing with edibles and food manufacturing. Here are a few simple ways robotics can help create eco-friendly assembly lines
1. Better Packing
The latest robotic case packing machinery is equipped with technology that can pack edibles with less plastic than manual packaging. Reducing the amount of single-use plastic waste required to get food items from factories to consumers’ homes safely.
They can also load pellets with more efficiency than possible manually. That means less fuel spent on transporting goods to warehouses and supermarkets.
2. Fewer Errors
To err is to be human. That’s not a great quality to have in the food packing industry when your error could mean improper seals, food recalls, spills and spoilage. Robotic case packing machines come laced with sensor technology. That enables you to check for seals before products head to the secondary packaging department.
Fewer errors in the factory mean less finished goods wasted and less time spent on fixing these errors. That also mitigates the risk of a product recall which can cause a company severe losses.
3. Less Waste and Spoilage as Food Moves Down the Line Quicker
Your human workforce can only work so fast, even if they are highly skilled. The speed of robotic packers, however, is unmatched. An excellent quality to boast about when dealing with perishables that come with a ticking clock.
Automated packing can reduce the time edibles are left exposed to different contaminants and fluctuating temperatures in the assembly line.
Also, fewer human hands touching food means less risk of bacteria and viruses making their way into food packages. That helps cut down on the amount of food ending up in landfills. It also helps to reduce the 170 million metric tons of carbon dioxide created by food waste annually.
4. Fewer Employees Driving to Work
More automation means less dependency on employees. Even the teams you hire to supervise your factory can work remotely and can still stay on top of things. With robotic case packing, you can keep tabs on your assembly line from pretty much anywhere. Meaning employees don’t need to drive to the factory's physical location as frequently.
That can simultaneously help curb costs, decrease carbon emissions and run operations more effectively.
5. AI Integration
Artificial Intelligence integrated robotic case packing systems mean more feasible packaging options for your brand. AI can process statistics and automatically adjust the volumes of products that need to be processed.
System-wide data analysis can pinpoint precisely what is needed where. That can cut down on wasted resources and avoid over-stock by checking production quantities based on demand. All with a few tweaks in the software and without the need to hire extra staff.
6. Increased Consistency
Robotic case packing can package your product faster and consistently. That results in less wasted packaging material. Consumers can expect a more consistent product from your brand when robotic case packers are a core part of your assembly line.
7. Easy Modifications
Training staff is often a considerable expense for any company. Robotic packers can be used to package different items with a few simple software modifications. Making them multi-functional and reducing the need for purchasing multiple packing machines.
8. Energy Efficient
Robotic case packers can help make your end-of-the-line packaging process energy efficient. As opposed to pneumatic machinery that used compressed air technology. Pneumatic machines use significantly more energy to operate. They also need replacement parts more often. Robotic case packing uses less energy and is more versatile in its range of functions.
Designed for Tomorrow and Today
Adopting environmentally positive practices is not just more productive, it’s also more profitable. Robotic integration can give your factory flexibility and decrease the negative impact on the environment.
Automation can help increase resilience against many threats faced by industries as we rebuild our economy after the Covid-19 pandemic. With increasing customer emphasis on sustainability, robotic case packing can be the answer.
To invest in your manufacturing unit's future and make it more environmentally sustainable, contact BluePrint automation today.