Exploring Advancements in Case Packing for Your Plant
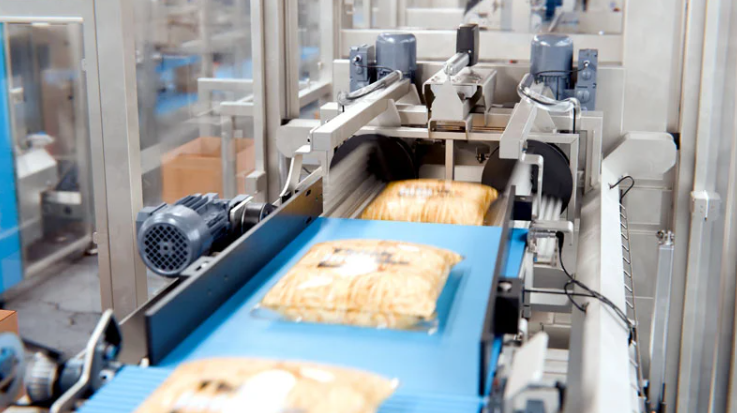
Innovation is driving new styles of case packers with groundbreaking advancements that require less operator intervention and enhance packing versatility. Executives in the packaging industry are even buzzing about how these advancements can uncover new possibilities and transform operations.
Still, these breakthroughs can be offset by choosing a case packer that doesn’t quite fit your needs or is too difficult to operate or maintain, which is still very common, especially for companies starting with automation.
We will share some industry-wide advancements and explain why flexibility is essential to getting the most out of your case packing system. We will then provide examples of how BluePrint Automation partners with customers to align their needs with tried-and-true solutions that effectively utilize these advancements.
Recent Advancements in Case Packing
We asked our Sales Team three years ago about advancements in case packing they’ve seen in the industry. Among the advancements they cited was the integration of different styles of robots to create new case packing machines, like the Spider 300v, to increase packing versatility and efficiency.
These integrated systems have only become more advanced, with AI and other innovative technologies allowing producers and co-packers to incorporate more packing styles and variety packs into their operations while simplifying controls and enhancing safety and maintenance.
Artificial Intelligence: Recent advancements in AI and robotics promise to improve quality control in vision systems, increase packing capabilities, support robust predictive maintenance, and enhance overall throughput.
HMI and Controls: Innovations have enabled packaging machinery manufacturers to design HMIs that help anyone interacting with the case packing system become familiar with operating and maintaining it. As turnover is high in many plants, these manufacturers can implement various controls and tools to support safety and operability for even the least experienced operator.
Why Flexibility Might Be the Most Important Factor When Choosing a Case Packer
While some machinery manufacturers have focused on developing new advanced systems with all the bells and whistles, BluePrint Automation has optimized our tried-and-true case packers with more options and support to meet our customers’ production needs. This has enabled us to offer multiple pathways for our customers to proceed and benefit from these innovations without affecting other parts of their operations.
Since we specialize in many different styles of case packers, we can use our experience and expertise to offer a tailored solution, like an all-in-one system for limited space and maximum performance or a modular system versatile enough to support evolving packaging needs.
However, procuring the proper case packing solution industry-wide can be difficult as some OEMs specialize in only a few types of case packers, limiting options. Also, customers might not know exactly what they need and purchase a system with too many or irrelevant features, creating more headaches.
How to Avoid the Pitfalls of Choosing the Wrong Case Packing System
Companies can struggle with an automated system they purchased that doesn’t align with their business goals, plant layout, or operator experience running the machines. It could even lead to “brittle automation,” where productivity increases when the system is running correctly, but process flexibility decreases because:
- The system was too expensive upfront, and the producer must find ways to justify the investment.
- Few system champions are available to train new operators and technicians because they leave a few months after implementation. We sometimes call this the “train drain.”
- Adjusting to new recipes and packaging requirements may require significant maintenance and downtime, bringing operations to a halt.
In the first of a three-part e-book series that examines automation justification and implementation in the CPG industry, Packaging World interviewed experts on how companies could avoid brittle automation. This was inspired by an HBR article that explored this phenomenon in various manufacturing settings throughout the 20th century.
The experts offered a financial justification checklist that can apply to any system implemented in a manufacturing plant: Any investment in secondary packing automation should align with business goals, have quantifiable benefits, and address pain points.
As such, companies should also take a bottom-up approach to ensure operators, technicians, and other floor personnel can voice their opinions and let management know what they need, as they will interact with the machines daily.
Ensuring Flexibility Through Innovation Backed By Expert Consultation
Many of our case packing solutions offer the advancements and features we described. BluePrint Automation is a very diverse company, and our team listens and reacts to customer challenges by taking them down relevant pathways that address many different cases, counts, and needs. We will also ensure floor staff have the training now and later to operate and maintain the selected case packer.
While more companies are expanding their capabilities through technological advancements, we have a leg-up in this area because we have always been doing it this way.
- In one instance, we devised a variety pack solution that combined our Gravity 100r case packer and bulk feeding system to optimize run speeds and the equipment's compactness. Our experience in robotics and gravity allowed us to recommend an innovative, inexpensive, and very flexible solution to the customer.
- Additionally, we are getting ready to roll out a new version of the Spider 200i that can run left-handed and right-handed cases for producers and co-packers who may have to deal with diverse, shorter runs. This advancement of our existing system will ensure customers can run both on the same machine to maximize packing efficiency and revenue.
- We also developed an alternative approach to building display-ready pallets that automates the process using our Gantry 300 SWING to stack three-sided display boxes. This minimizes labor, space, and time devoted to manually constructing display-ready pallets on the floor while meeting consumer and retailer demands.
Wrapping Up
Customers can and should identify their strategic business objectives and pain points to determine the quantifiable benefits they need from their case packing system. Yet, they shouldn’t have to choose a system on their own. Our sales engineers will ensure you are presented with all the information and pathways you need to make the best decision for your business and people.
So many exciting advancements and innovations in case packing are making automation a viable option for producers and co-packers of all types and sizes. Let’s explore what you need from your case packing system to get the most return from your investment. Contact our sales team today to get started.