Case Packer Safety and Sanitation Design
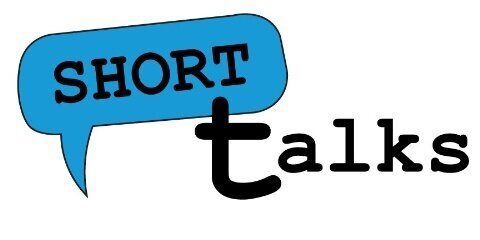
Mike Rebollo
Southwest Regional Sales Manager
BluePrint Automation (BPA)
What are some of the most important modern requirements for sanitation accessibility that case packers should feature? How do BPA machines incorporate them?
One of the most important features is accessibility to the areas that require cleaning. It does not matter if the machine is Stainless steel washdown or painted mild steel non-washdown, if the operators and sanitation crews cannot get the tight areas, then there will be sanitation problems.
Another common feature is to use stainless steel for the frame. Many of our models are available in both painted mild steel and stainless steel
BPA incorporates easy access concepts on all our equipment. This comes in many forms from frame design, safety door design, to conveyor designs. The designs will vary depending on the needs of the environment, (washdown vs. non-washdown). For example, on washdown we often incorporate conveyor tilt tails; non washdown we have open frame designs that allow good floor access and operator access.
Why is sanitary design so much more important now for food processors in packaging?
Sanitary requirements continue to increase for food processors for the safety of the public. Many of these requirements are cleaning procedures, new sanitary designs and materials allow for ease of clean up and minimizing areas for product build up.
How did BPA keep sanitary design in mind when designing your machines?
The number of requests and requirements for sanitary design has been increasing for several years, consequently, these concepts are a high priority for BPA as we come out with new models and make improvements on existing models. Our Spider 200i is a prime example. This model is a couple of years old and incorporates many sanitary design features.
How does sanitary design and easy accessibility of a case packer increase production rates by limiting downtime for cleaning and maintenance?
Sanitary design and ease of accessibility do not necessarily increase product rates. Production rates are determined by components and mechanical design. However, you are correct that they can increase overall daily output by reducing the amount of time required to clean and sanitize the equipment.
As equipment manufacturers, we cannot specify, nor assume how long it will take to clean and sanitize our equipment. Sanitation requirements and procedures are determined by individual production plants. Sanitation times will vary a great deal based on the products manufactured and plant requirements.
Throughput rates are based on processing equipment out puts. At BluePrint Automation we work with bakeries and snack companies that are running multiple shifts and have outputs speeds of 25 – 2500 products per minute. Let us know what your requirements are and we will be able to handle them.
Has COVID affected how people look at sanitary design in packaging? How do your machines help customers deal with the added sanitation concerns?
COVID has certainly affected how we look at sanitary requirements in all areas of our lives. Machinery design and packaging design are no exception. Our designs allow for ease of cleaning which allows food manufacturers to have confidence that their BPA equipment can be appropriately cleaned and sanitized for their employees and customers. The need to keep the work environment clean and sanitized for the health of the company’s workers is a majority priority for all companies during this pandemic.