Applications of Robotics Technology in Secondary Packaging
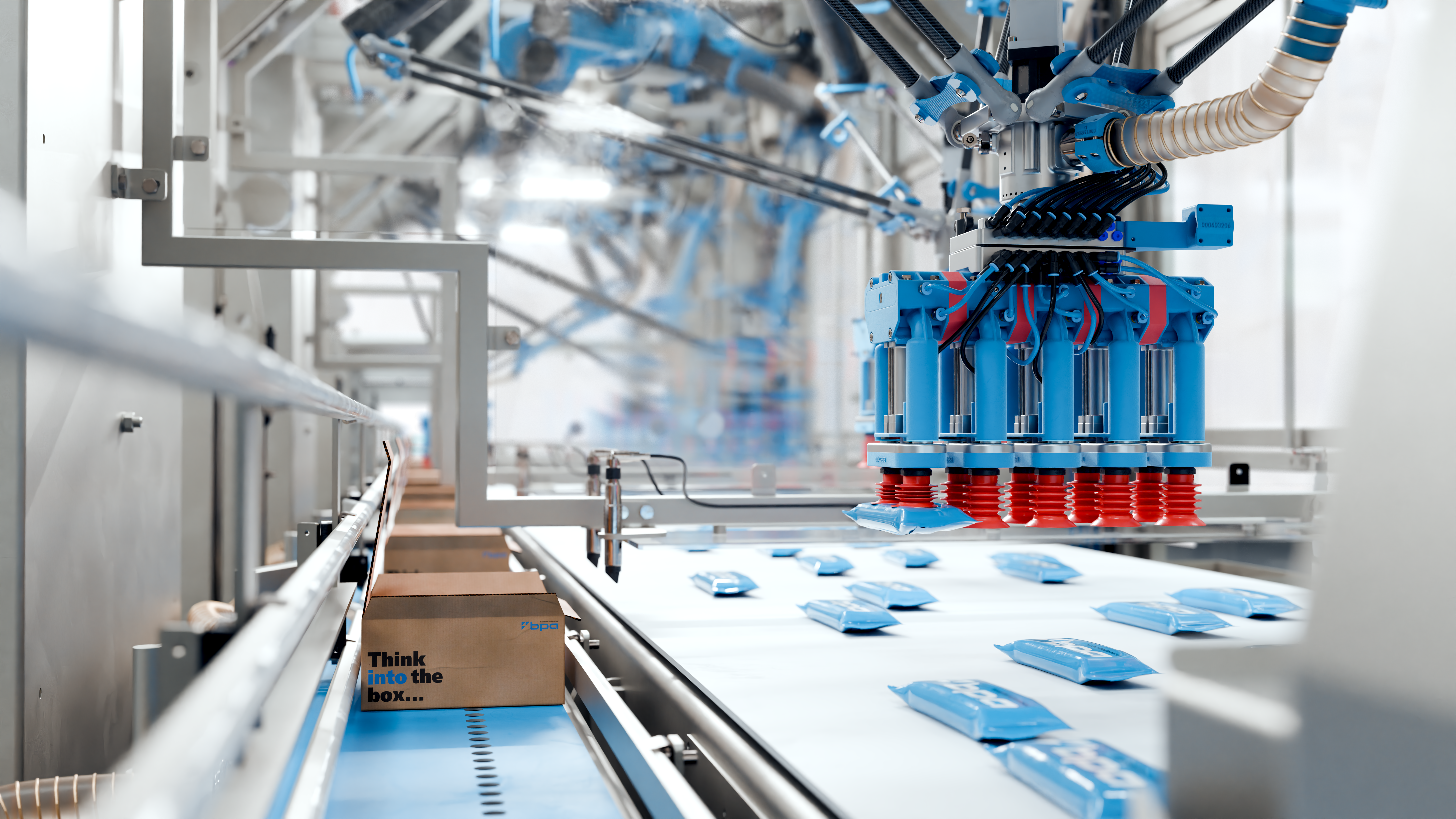
Robotics have transformed how food and beverage manufacturers meet high-speed production goals while ensuring consistency and reliability. This is part of an industry push for increased automation of downstream operations to streamline tasks and reduce reliance on manual processes.
Human error, the high costs of labor, and production demands have all contributed to this push by manufacturers toward automation and robotics. Robotics bring speed, versatility and precision to secondary packaging operations, ensuring products are correctly and safely packed for distribution.
We will examine some of the most common applications of robotics and explore their benefits and some limitations, too.
Types of Robots Used in Case Packing
Robotic systems excel in high-speed, high-volume environments where flexibility and scalability are crucial to keep up with demand for a wide range of product runs. Packaging requirements are growing more diverse with complex pack patterns and new materials. Robotics can provide the accuracy and consistency required in these environments to meet a manufacturer’s needs.
While we generally refer to delta robots and six-axis robots for secondary packaging applications, cobots are also slowly being introduced to packaging operations.
Delta robots feature a spider-like design with multiple arms connected to a base for high-speed picking and placing applications, including lightweight products like pouches, granola bars, and single-serve snack bags. They are also ideal for variety packs. They are best suited for lightweight, repetitive tasks that require minimal payload capacity.
Six-axis robots have versatile arms capable of movement in the x, y, and z directions, mimicking how a human arm would move. They are much slower than delta robots but can handle heavier payloads and have a wide horizontal and vertical reach. They are best suited for applications that require heavy or mixed-sized cases or flexible movement in all directions. They are also often used for palletizing and can be mounted or moved much more easily than delta robots.
Cobots are not traditionally used in the food & beverage industry for case packing. However, they are slowly being introduced to provide a one-to-one replacement for humans when needed. They bring flexibility and safety in tight settings, offering a much smaller footprint than delta or six-axis robots. They are much slower than other robotic systems, though, so they’re better suited for palletizing or tasks that require gentle handling or repetitive movements rather than high-speed case packing applications.
Four Examples of Robotics Used in Secondary Packaging
- Variety Packs: Delta robotic systems can pick and place products from a bulk pile. They streamline sorting, orienting, and positioning tasks to meet high-speed demands with accuracy. They can simultaneously handle different product types and arrange them in pre-programmed patterns for consistency and flexibility.
- Bulk Products: Six-axis robots are good at handling oversized, heavier items, seamlessly lifting and loading bulk products into cases. Their extended reach and multi-axis flexibility enable efficient case packing for mixed-weight items, like large beverage cartons or mixed-case bundles.
- Tray Loading: Delta robots can quickly load individual items into trays. Using vision guided systems, they can pick, orient, and place items like pouches or snacks into pre-arranged tray slots, ensuring accuracy in high-speed, repetitive packaging lines.
- Quality Control: Vision guided robotic systems can also be programmed to inspect items as they are fed into the system, identify and remove defective products, and ensure proper placement and the correct product count before they are packed into cases, improving quality control and presentation.
Benefits of Robotics for Your Packaging Operations
Reducing Manual Tasks: Robotics and automation, in general, can complete repetitive tasks and reduce the physical strain on workers, especially when handling heavier payloads or high-demand runs. Robots don’t get sick or require breaks, enabling manufacturers to achieve higher productivity and promote a healthier work environment.
Adding Flexibility to Your Line: Robotic systems offer much quicker changeovers than manual systems, allowing manufacturers to change runs in 30 seconds rather than 30 minutes. This eliminates unnecessary downtime and allows manufacturers and co-packers to handle more diverse packaging formats and product runs.
Scaling Your Operations: Robotic systems also offer the scalability to grow alongside production demands. Robotics can help manufacturers adapt to market changes, supporting sustainable growth and evolving packaging requirements. AI and software programming advancements can increase real-time flexibility and the capability to handle diverse product runs at higher speeds as those demands are realized. They can be integrated relatively easily into an existing line, too.
Limitations of Robotics on the Line
Your team should consider some limitations with robotic systems before implementing them, including initial investment costs and space constraints. For example, guarding and other safety features for robotics require space that may be unavailable in some plants.
Some applications may be more suitable for certain systems than others, like high-speed runs for delta robots and heavier payloads for six-axis robots. Specific applications with irregularly shaped products or complex orientations may be better for human operators to handle.
Manufacturers have strived to make maintenance for robotic systems more straightforward and user-friendly. HMIs are more usable and can alert an operator to any technical issue that should be addressed. Innovations like QR codes also make it easy for operators to get support. Still, some technical expertise and regular internal maintenance are crucial for long-term ownership, which may be prohibitive for smaller manufacturers.
How BPA Supports Your Vision for Robotics
As a leader in case packing solutions, we specialize in designing robotic systems tailored to each customer’s packaging needs with a focus on flexibility, safety, and performance. We’re dedicated to ensuring that our systems perform reliably and meet our high efficiency and quality standards.
- We offer custom engineering solutions and partner with some of the most intelligent people in the robotics industry to advance our equipment further.
- Our systems meet immediate functional needs and are designed with future flexibility in mind to accommodate potential product and packaging changes and company expansions.
- We offer training programs, remote technical support, and scheduled maintenance visits with a dedicated sales engineer to ensure optimal performance of your robotic system, identify potential issues, and address maintenance gaps.