The Checklist for Preparing Your Equipment Installation
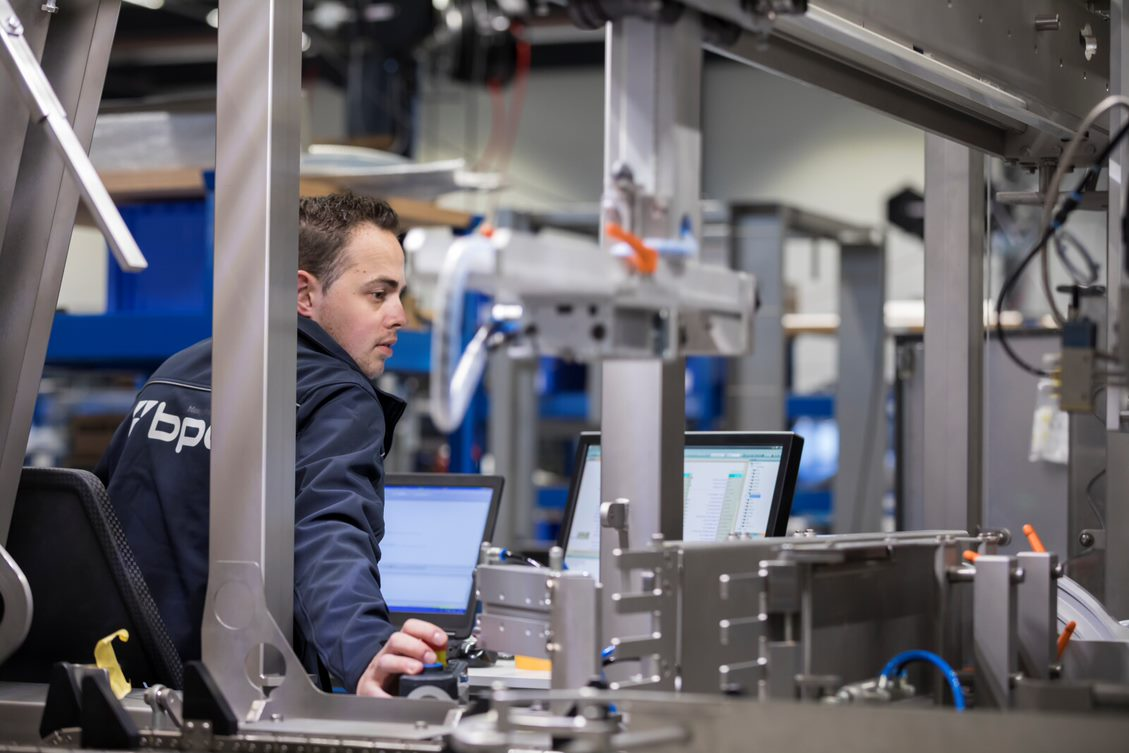
When you are installing new equipment such as a case loader or a tray packing machine, it can lead to a fair amount of trouble if you are not prepared for it. Mistakes can lead to downtime, which can be very bad for business.
This is why checklists are essential to make sure that everything is going smoothly. Check these every time you have new equipment installed:
1. Talk to the Project Manager
Before you even begin to make any installation, you should talk with your project manager first. Packaging automation, for instance, can be tricky, so you need to have all the relevant information at hand. The project manager will likely have the answer to your questions, so you may want to get all the information you need before proceeding.
2. Determine the Floor Thickness
You may think that the floor does not matter – but the truth is that it’s quite relevant. Multiple pieces of equipment will deal extra force to the floor, so you need to make sure that the floor is reinforced enough to handle it. For example, a robotic case packing unit can send a lot of pressure through the floor, which means you’ll need an extra 8 inches of floor reinforcement.
3. Find Out About Environmental Conditions
Depending on the piece of equipment that you have installed, you should make sure that you meet certain environmental conditions. If the environmental conditions are not up to par, it might make things difficult for the technician installing the unit. Talk to the service technician and inform them if there are any unusual environmental conditions in the place you are installing the equipment.
4. Gather the Necessary Supplies
When installing equipment, you’ll need a couple of tools. If a technician is installing the piece of equipment, the chances are that they will bring their own tools to make the installation. However, if you are the one installing a product-handling piece of equipment, then you must make sure that you gather all the installation supplies necessary.
You may also want to be sure about specific requirements that may be required, such as power outlets or communication cables. By knowing everything beforehand, you will be able to prevent potential delays.
5. Drop Sites of the Equipment
There is a big difference between dropping off the piece of equipment at the entrance and doing it in the place it’s supposed to be installed. For instance, if you are installing an automatic cartoning machine and know exactly where it is supposed to go, you may want to arrange the drop site with the supplier.
This will end up saving a lot of time and may also protect your new equipment. The last thing you want is to damage it simply because you handled it poorly.
6. Check Piping and Surrounding Items
When replacing an old piece of equipment with a new one of the same line, you may not have to deal with relocations and other changes. However, if you are replacing an old case packer with a newer, fancier automatic case packing unit, then you should consider the surroundings.
Do you need new piping? Perhaps you’ll have to work on fresh electrical wiring. Do you have enough space in order to place the new item there? Make sure that you jot these things down beforehand, as thorough preparation will reduce your downtime.
7. Ensure the Floor Is Aligned
The last thing you want is to install an expensive robotic packaging automation unit, only to find out that it continuously slides on the floor as a result of pressure. This usually happens with robotic units that have not been installed on level ground.
For this reason, you must make sure that the area is properly aligned and leveled. You might need to install a level concrete pad, along with an aligned anchoring system. This will ensure the piece of equipment stays exactly where it is supposed to.
8. Consider Storage Options
There is a good chance that the installation may not go exactly as planned and you’ll have to put your new equipment into storage. Perhaps the environmental factors are not ready, or you simply cannot have it installed by the originally planned date. In that case, you must arrange for storage. Make sure that you have a dry place ready for you to store the item, preventing deterioration. Even if you don’t think you’ll need it, it can’t hurt to take this precaution.
9. Schedule Safety Courses
Not all pieces of equipment are the same. If you buy a new case packaging system, for instance, there is a high chance that it will be different from the one previously used. While this may mean new benefits, it might also mean new dangers – dangers that your workers should be aware of.
If possible, talk with the suppliers about providing safety training. You may also want to make sure the training takes place at least one day before installing the unit, as this will reduce downtime.
10. Schedule a Follow-Up Visit after Installation
After installation, you might want to schedule a follow-up visit. You need to make sure that everything is working how it is supposed to. It will also help the learning curve of the workers, as they will see the piece of equipment operated firsthand by a professional.
This step is particularly important to check if you go from a manual to a robotic case packer, for instance. As the technique changes, you need to make sure everything is in order.
The Bottom Line
Installing equipment may take a bit of planning, to make sure that things go smoothly. This is why a checklist is necessary, to ensure you don’t accidentally miss anything. By being thorough, you should be able to reduce downtime and increase productivity.